Mastering Horizontal Flow Wrapper Machines: A Comprehensive Guide
Horizontal flow wrappers are invaluable tools in the packaging industry. But how exactly do these machines work? And what should you consider when choosing one for your production line? This post will teach you everything you need to know about horizontal flow wrappers.
Whether you’re looking to improve your existing wrapping processes or research these machines for the first time, you’ll find value in the information below. Let’s get started!
Table of Contents
Introduction
Horizontal flow wrapping, also known as horizontal form-fill-sealing, is an automated packaging process used to wrap products in flexible packaging materials. It’s a widely used packaging technology. It’s found in various industries, such as food, pharmaceuticals, cosmetics, and consumer goods.
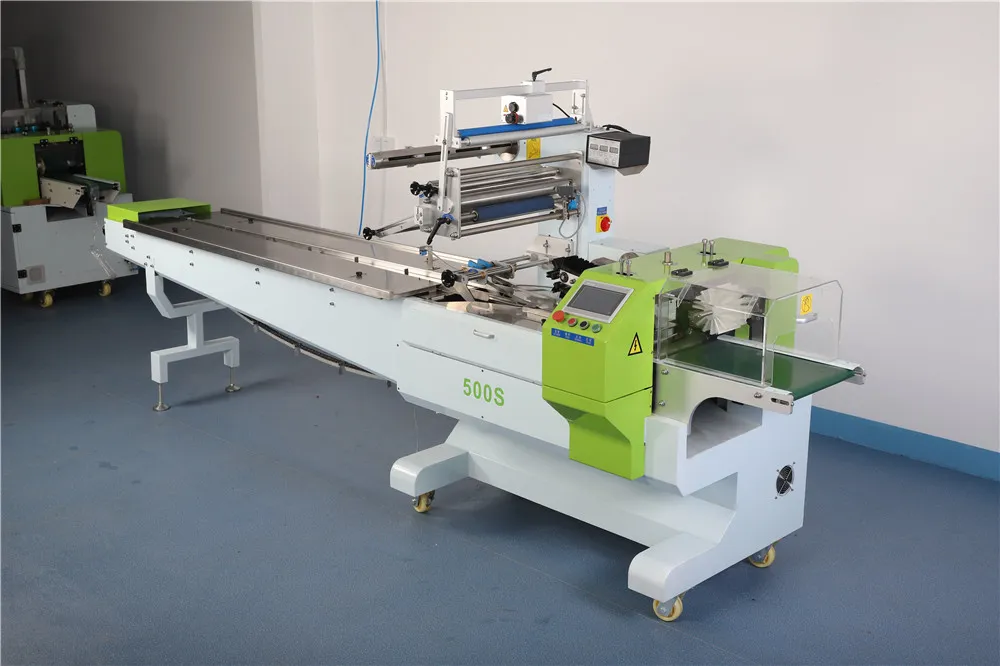
The benefits of horizontal flow wrapping are immense. These machines allow high-speed, high-volume packaging critical for meeting consumer demand.
Packages are consistently sealed to maintain product freshness and prevent tampering. And flexible films reduce material costs compared to other packaging options.
With so many advantages, it’s no wonder horizontal flow wrappers are a staple in packaging operations worldwide.
Mastering these machines opens new doors for your products. You can expand into new markets, reduce labor costs, and strengthen your brand image with professional, eye-catching packages.
This guide breaks down everything from choosing equipment to optimizing your wrapping processes. Let’s explore the incredible possibilities of horizontal flow wrapping.
How Do Horizontal Flow Wrappers Work?
Horizontal flow wrappers seal products in packaging film using an automated, multi-stage process. Simply put, products are fed into a machine, wrapped in film, and sealed into packs. But how exactly does this horizontal wrapping process work? Here, we’ll break it down step by step:
1. Product Infeed
The process begins with an infeed conveyor transporting products into the machine. Devices like timing screws or chain transfers synchronize the flow of products for consistent wrapping.
2. Film Unwinding
Packaging film stored on a roll is unwound and fed into the machine through tension control bars and rollers. This advances the film through the wrapping system.
3. Product Wrapping
The product and film merge and sealing jaws fold the film around the product to create a tube-like package. Flow wrappers can wrap products from all sides or leave some areas unwrapped depending on the machine style.
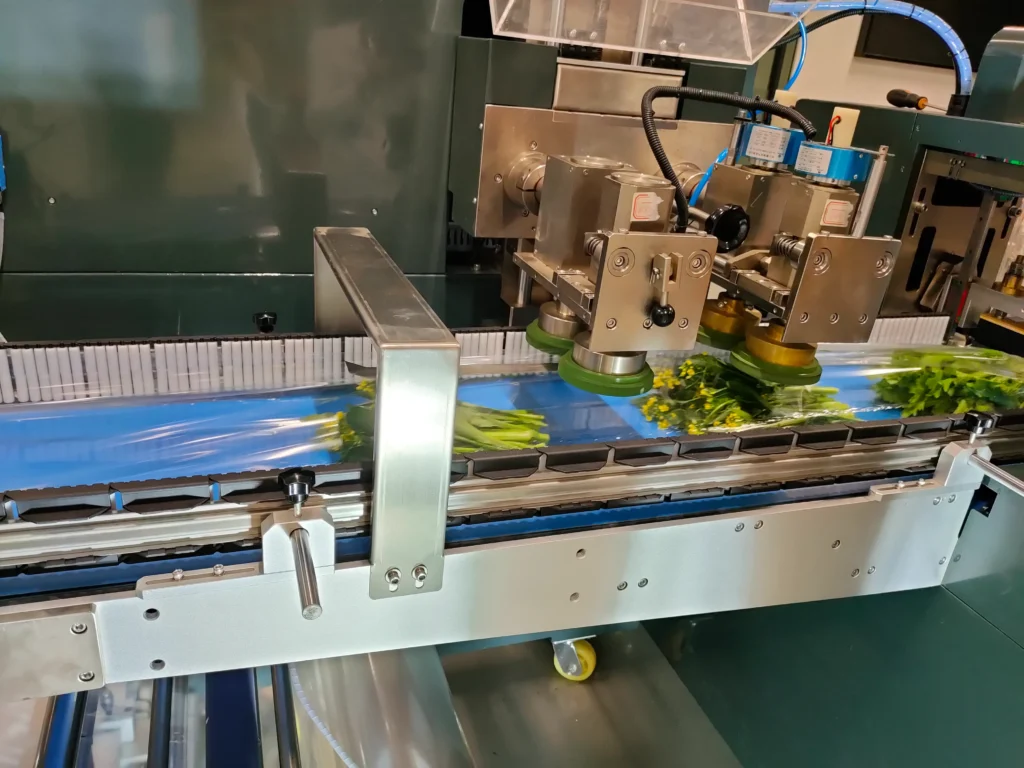
4. Cross-Sealing
Sealing jaws then seal the leading and trailing edges of the package with heat or pressure. This forms an airtight seal across the width of the package.
5. Severing
A blade severs the sealed packs between products to create individual packages. The packs then exit the machine.
6. Additional Features
Machines may integrate date coders, or label applicators to add further functionality.
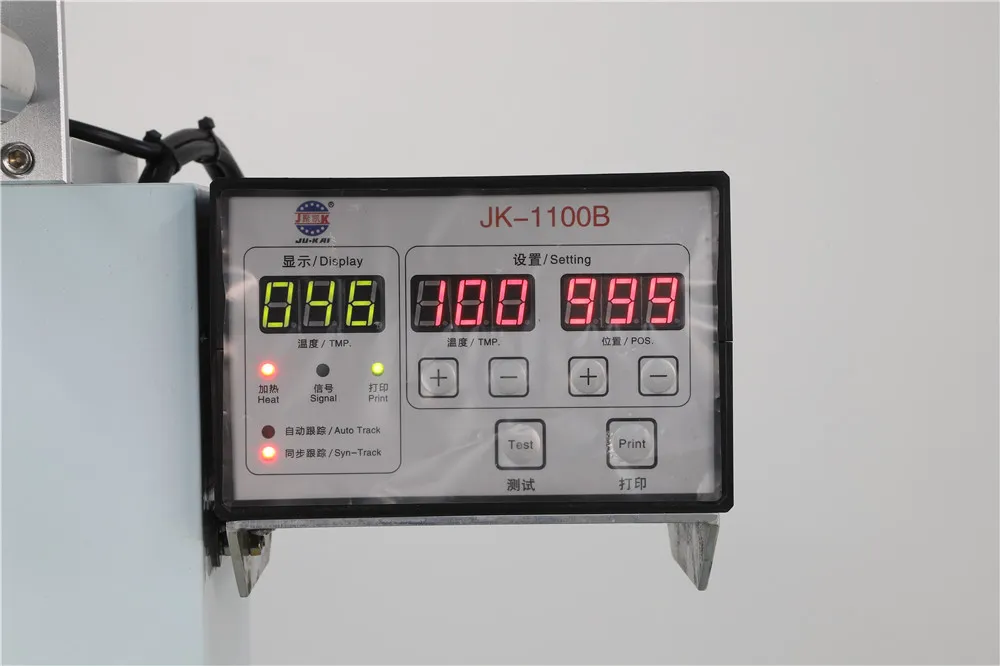
Once you understand these fundamentals, you can optimize horizontal wrapping for any product. Next, we’ll explore the different types of horizontal flow wrappers available.
Types of Horizontal Flow Wrappers
There are two main styles of horizontal flow wrappers – intermittent motion and continuous motion machines:
Intermittent Motion Wrappers
Intermittent, or reciprocating motion machines operate in a stop-and-go method. The product feeds meter the products into the machine one at a time. The process pauses as the machine wraps and seals each pack before advancing.
Advantages:
- Precise control for wrapping delicate products
- Ability to wrap multicomponent products
- Simpler, lower-cost machines
Disadvantages:
- Slower speeds
- Higher mechanical wear from constant stopping/starting
Continuous Motion Wrappers
In continuous wrappers, the product flow and machine motion are non-stop. Infeed systems gently accelerate products to match the machine’s constant velocity. As one package leaves, the next is already being wrapped.
Advantages:
- High-speed wrapping up to 300 packs per minute
- Maximum throughput with round-the-clock operation
- Lower maintenance from lack of start/stop motion
Disadvantages:
- Difficulty wrapping unstable or delicate products
- Larger footprint from extended conveyors
- Higher machine cost
The volume, products, and budget of your operation will determine the best type of wrapper. Properly matching the machine to your needs is crucial. Next, we’ll explore the components that make up these wrappers.
Key Features and Components
Horizontal flow wrappers share common components that enable the wrapping process. Understanding these features is key for properly operating and maintaining your machine:
Infeed System
Gently meters products into the machine with inconsistent positions and spacing for reliable wrapping. May include conveyors, timing screws, separators, and transfers.
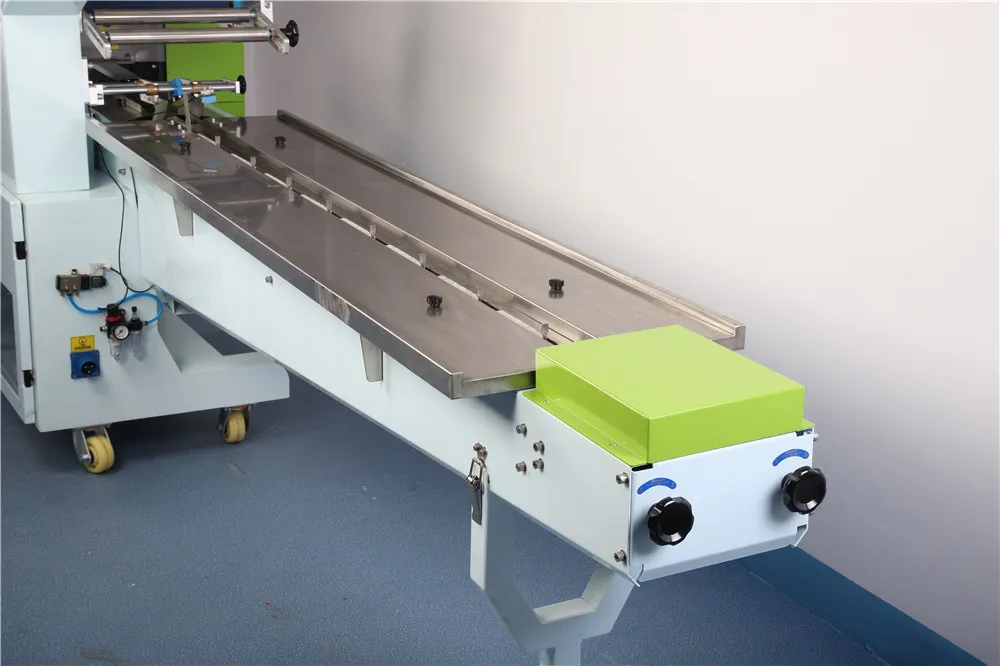
Film Delivery System
Controls film unwinding from rolls mounted on shafts or arms. Consists of film rollers, tension controls, and guiding components.
Bag Former
Folds the film around the infeeding product and forms the initial tube-shaped package. Shaping plates progressively wrap the product.
Cross-Sealing Unit
Sealing jaws, powered by thermal, impulse, or ultrasonic energy, seal the leading and trailing edges of packs. A cutting blade then separates packages.
Discharge Conveyor
Removes finished packs from the machine. Then transport them for downstream processing and case packing.
Electrical Control System
The “brains” govern all machine motions and functions. Allows programming of recipes and parameters.

Sanitary Design
Stainless steel frames, smooth surfaces, washdown capabilities, and tool-free access panels facilitate thorough cleaning.
Safety Features
Guards, sensors, emergency stops, and lockouts prevent accidents and enable safe operation.
Understanding how these components work together is crucial for selecting the right wrapper and keeping it running flawlessly. Now let’s go over considerations for choosing a machine.
Choosing the Right Horizontal Flow Wrapper
With many machine brands and configurations available, selecting a horizontal flow wrapper involves weighing several factors:
Product Characteristics
What are you wrapping and how will it impact equipment needs? Assess product size, shape, weight, rigidity, orientation, multipacks, and more.
Speed and Throughput
Determine your required output in packages per minute. High-speed wrappers often use continuous motion. Intermittent works for lower volumes.
Package Size Flexibility
If you package many product sizes, look for quick and easy size changeover abilities.
Machine Integration
Ensure the wrapper seamlessly integrates with upstream and downstream equipment like labelers and case packers.
Usability and Control
Evaluate machine and software user-friendliness. Touchscreen HMIs and recipe storage offer control simplicity.
Budget
Weigh costs against long-term value. Higher quality equipment often offsets expenses through uptime and OEE gains.
Supplier Experience
Choose an established wrapping machinery manufacturer with proven food packaging expertise. Seek supply chain partners, not just equipment sellers.
Taking time to properly match your operational needs to machine capabilities ensures successful implementation. Next, we’ll go through a start-to-finish guide on operating horizontal flow wrappers.
Operating a Horizontal Flow Wrapper
While every horizontal flow wrapper is slightly different, following general procedures and tips will set you up for packaging success:
Step 1: Film and Product Loading
- Load film onto unwind shafts, thread through rollers, and connect to sealing jaws
- Adjust film tension and guides
- Stage product to infeed conveyor
Step 2: Seal Checks
- Initiate seal checks without product to verify proper temperature, pressure, and adhesion
Step 3: Tuning and Setup
- Select product recipe or enter settings
- Adjust conveyor speeds, separators, guides to optimize product flow
- Confirm ideal seal placement with test packs
Step 4: Production
- Launch full production run
- Closely monitor process for several minutes, make any final tweaks
- Periodically check seal quality on packs
Step 5: Film Splices
- As film reel depletes, prepare splice tape and reserve film roll
- Rotate shafts and quickly splice films when prompted
Step 6: Shift Changes
- Save current settings in recipe program
- Notify next shift operator of any issues
- Restart production using saved recipe
Step 7: Sanitation
- Clear line of product
- Remove film web, disassemble per sanitation procedures
- Thoroughly clean and sanitize all surfaces, parts
Following best practices for operation, troubleshooting, maintenance, and changeovers will maximize up-time and minimize waste. Let’s explore some maintenance tips next.
Maintenance and Care
To maximize productivity and lifespan, following scheduled maintenance procedures is a must. Here are key tasks to incorporate:
Daily Maintenance
- Visual inspections of components
- Check fluid levels
- Remove dust and debris
- Test all safety features
Weekly Maintenance
- Thorough machine wipe down
- Inspect conveyors, bearings, and chains
- Validate seals meet strength specifications
Monthly Maintenance
- In depth sanitation of all surfaces
- Seal replacement
- Software and firmware updates
- Test emergency stops
Quarterly/Annual Maintenance
- Complete machine disassembly, deep cleaning
- Replace worn parts like bearings and blades
- Update and calibrate software and controls
- Schedule technician servicing
While frequent maintenance requires commitment, benefits include 55% less unexpected downtime, 17% higher OEE, and 12% lower maintenance costs according to wrapping equipment manufacturer ARPAC. Proper care directly improves your bottom line.
Next let’s explore some top applications of horizontal flow wrappers across industries.
Future Trends in Horizontal Flow Wrapping
While horizontal wrapping is everywhere, emerging technologies make them more versatile and valuable:
Automated Changeovers
Quick-change tooling, memory presets, and change part tracking will minimize downtime between product changeovers.
Greater Customization
Digital printing integration will enable unique packaging designs for small batches, limited editions, and custom products.
Smart Diagnostics
IoT-connected wrappers will monitor components in real-time and predict maintenance needs before failures occur.
Aseptic Packaging
Machinery innovations will allow horizontals to produce aseptically-sealed food, beverage, and medical packages.
Sustainable Materials
Wrapper integration will accommodate more recyclable, compostable, and plastic-free materials as consumer demand grows.
Total Traceability
Advanced data collection will provide complete transparency from ingredient origin through packaging. This supports consumer trust and brand reputation.
The future of horizontal flow wrapping is bright. As technology progresses, so will the capabilities of these indispensable packaging workhorses.
Conclusion
We’ve only scratched the surface of mastering horizontal flow wrappers in this guide. These versatile machines deliver unmatched efficiency, flexibility, and reliability to packaging operations.
Understanding how horizontal flow wrappers work, properly selecting equipment, optimizing operation, and maintaining machines will maximize the value of your investment. Partnering with experienced suppliers will ensure your competitive edge.
Horizontal flow wrapping opens doors to meet production demands. Reduce labor, and breathe new life into products through professional packaging. Implementing or upgrading your wrapper solutions brings answers to many manufacturing challenges. The possibilities are truly endless.
Jason
I’m the author of this post, with over 10 years of expertise in the field. Should you seek insights or information about flow wrappers, I’m here to assist. Let’s connect and explore the world of packaging together.