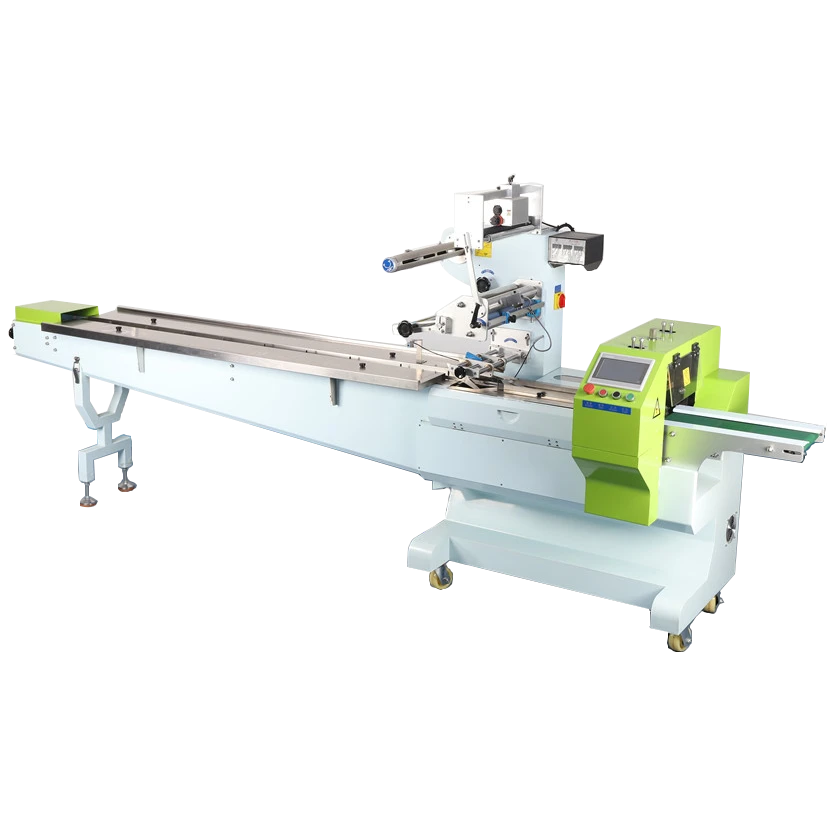
Flow Wrapper
Your Trusted Flow Wrapper Supplier
PACKAIM is one of the flow wrapper manufacturers in China. We are committed to being your supplier of high quality flow wrappers. From food to pharmaceuticals, our machines will wrap up a solution that makes your products pop on the shelf. With custom equipment backed by real industry know-how, we’re wrapping gifts for your bottom line. Let’s gift your business the packaging solutions it deserves!
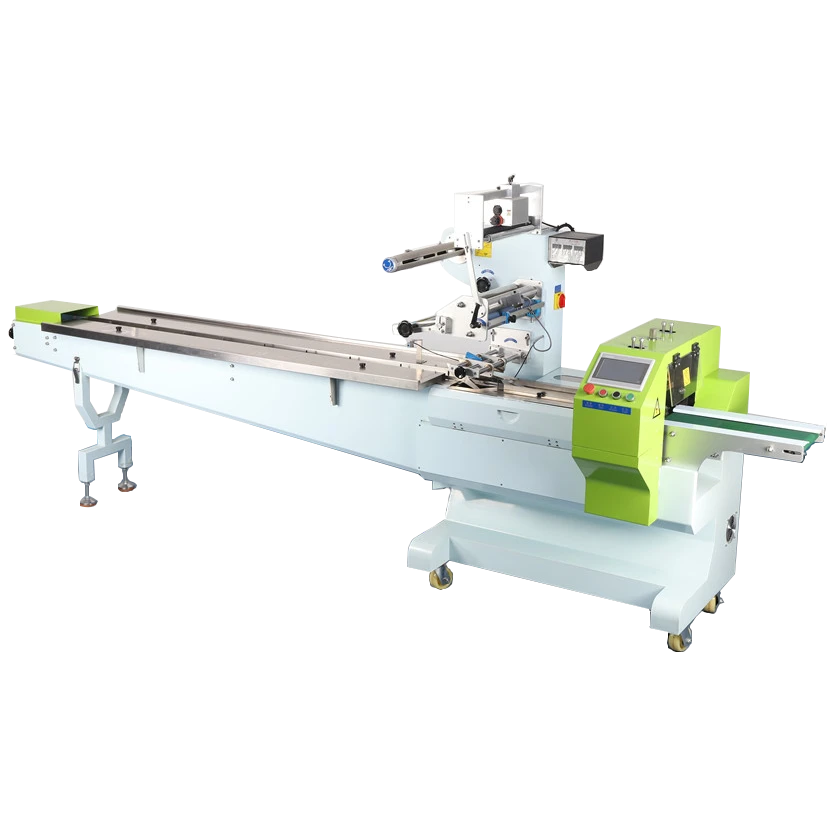
Flow Wrapper PAF-300S
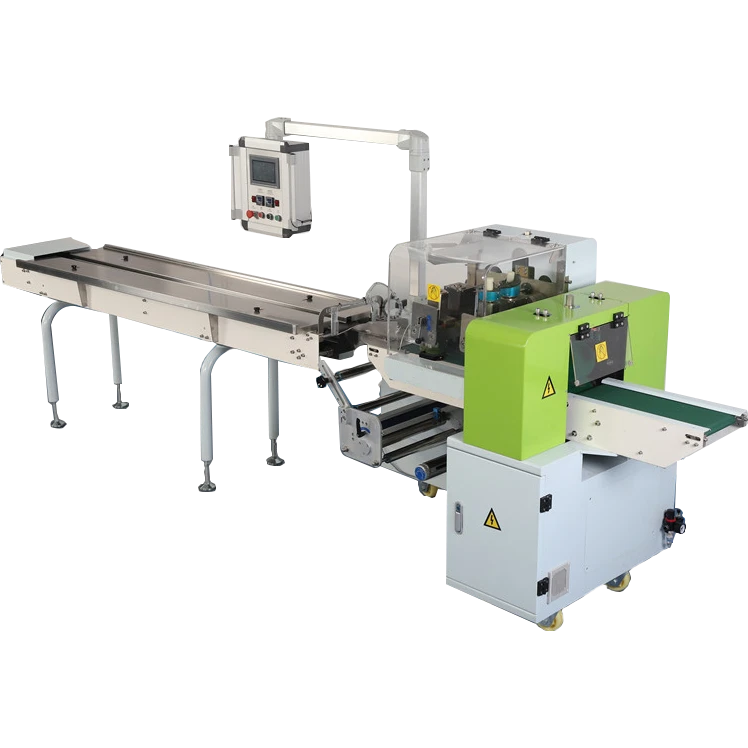
Flow Wrapper PAF-300D
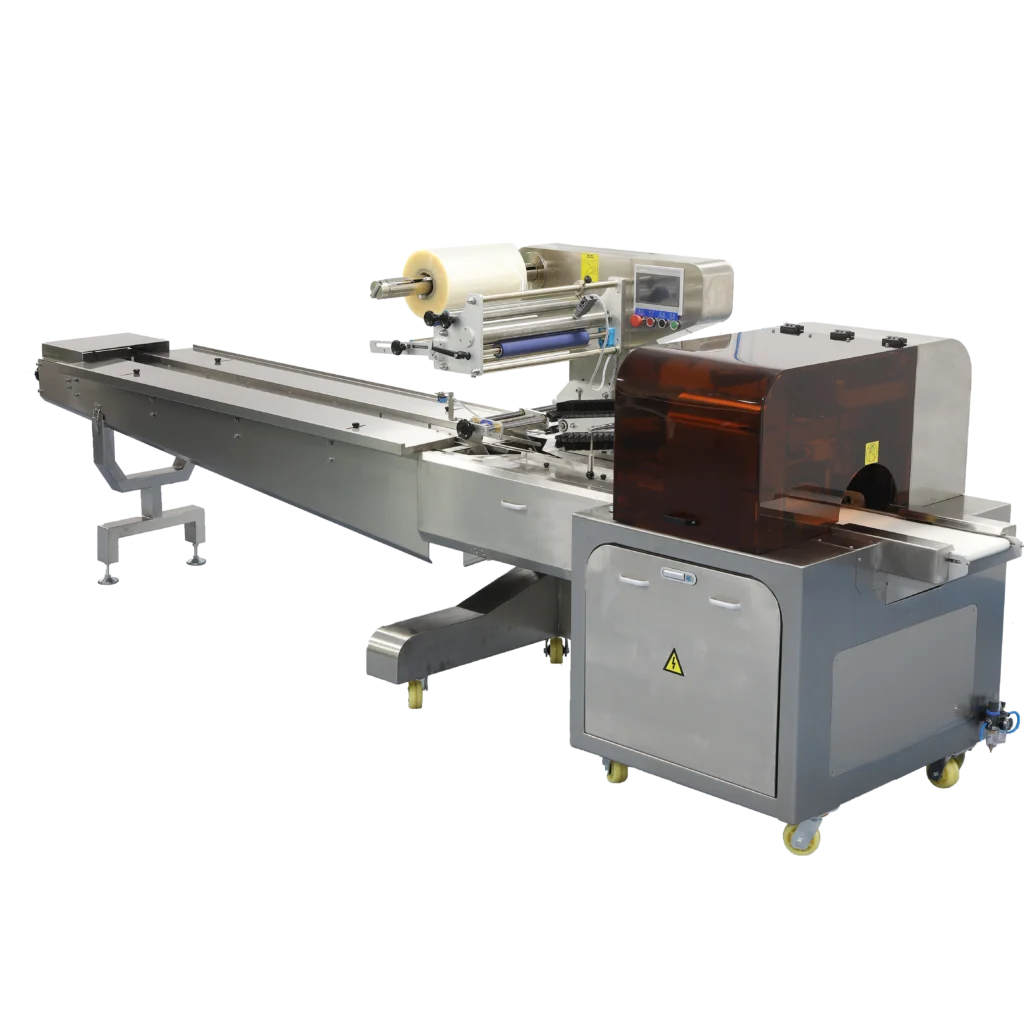
Flow Wrapper PAF-450
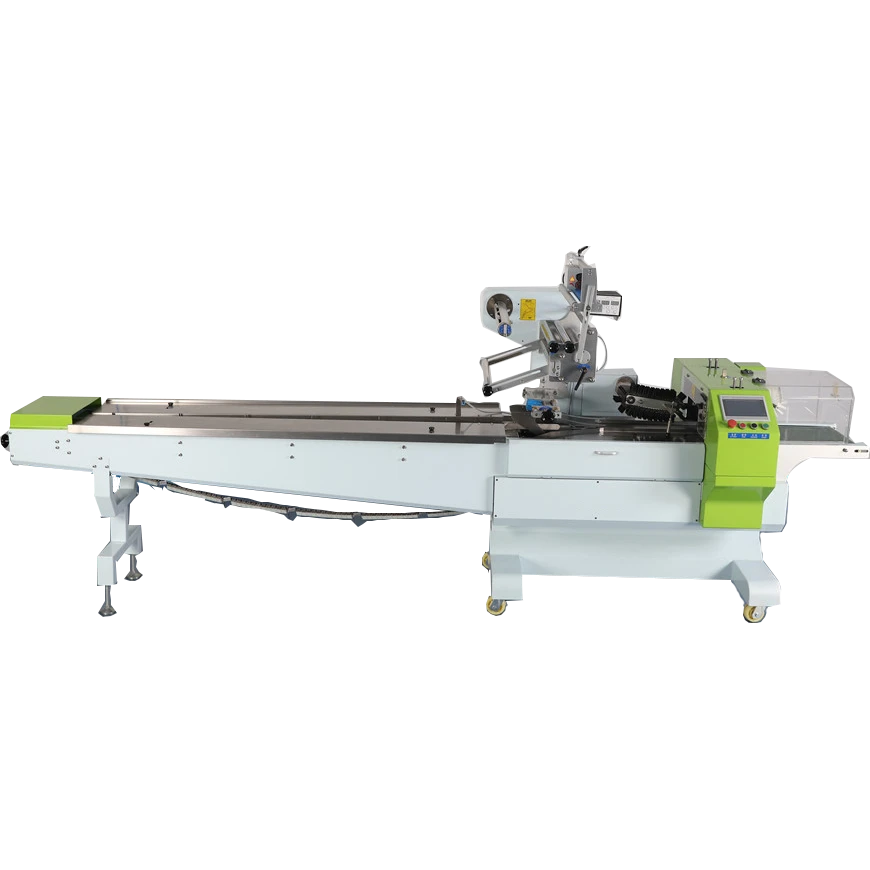
Flow Wrapper PAF-500S
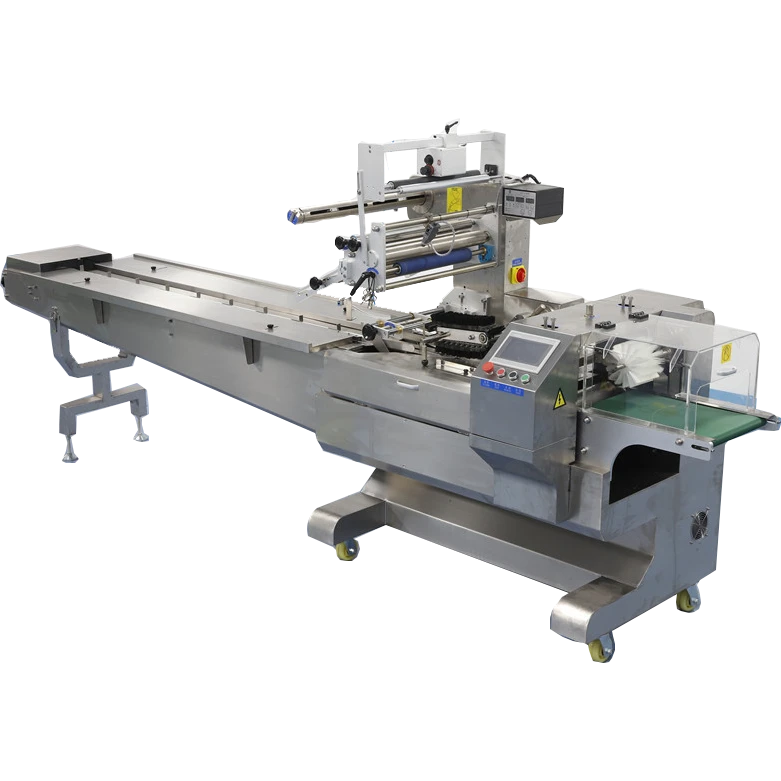
Flow Wrapper PAF-500SS
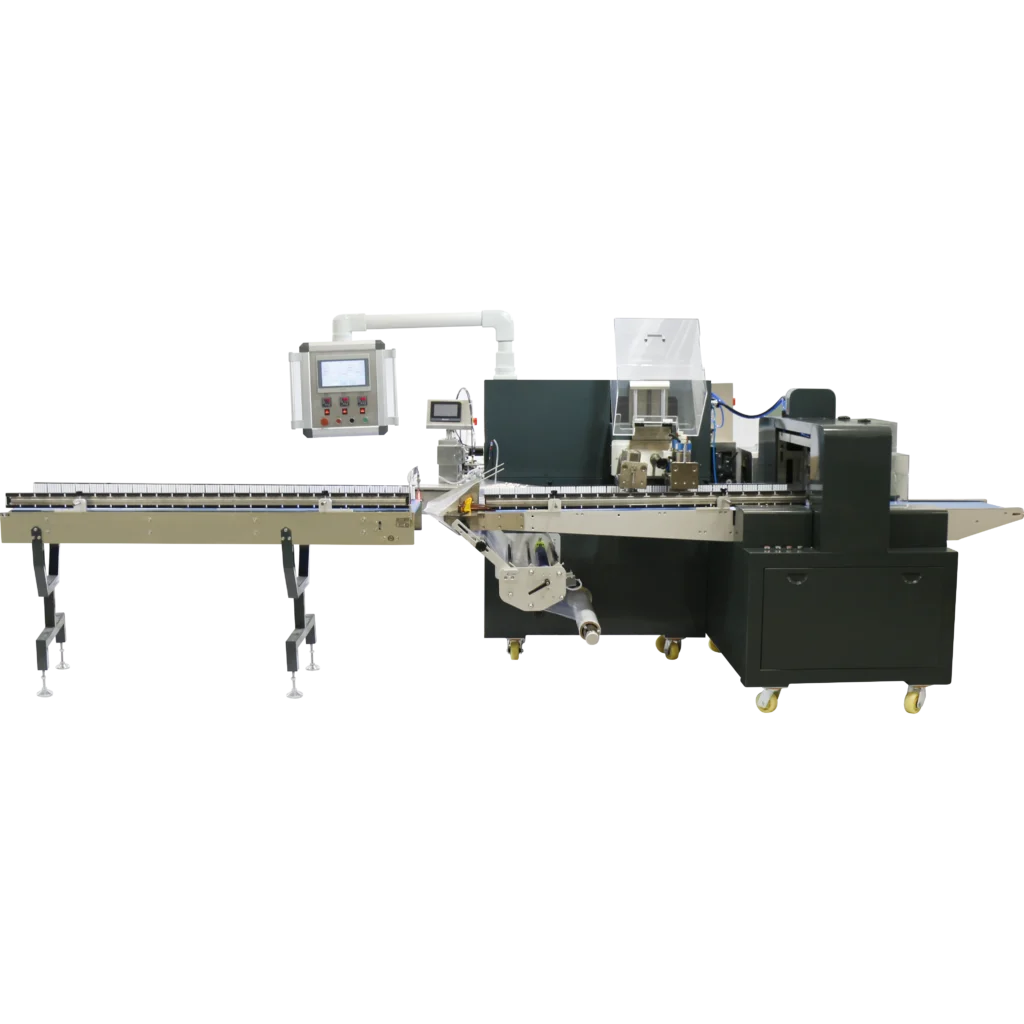
Flow Wrapper PAF-680
What Is Flow Wrapper
Flow wrapper is a packaging machine used for wrapping products in a flow pack or pillow pack. It is also known as a horizontal form-fill-seal machine. It functions by forming a bag, filling it with the desired product, and sealing it up.
Flow wrappers are designed to wrap a wide range of products such as candy bars, bakery items, frozen foods, and more.
The packaging process is called “flow wrapping” because the product is fed into the machine in a continuous flow, allowing for high-speed packaging. This makes flow wrappers an ideal choice for high-volume production lines where efficiency and speed are critical.
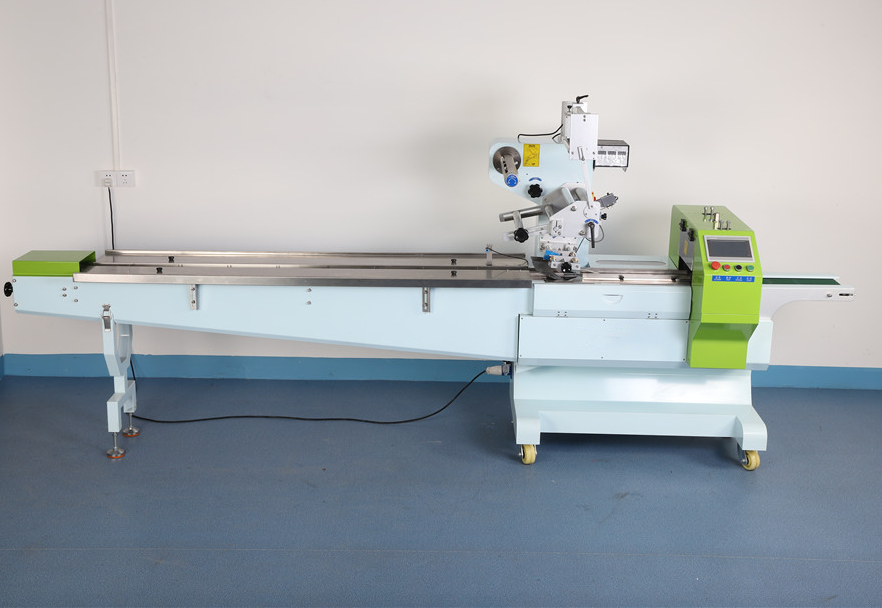
Key Components of Flow Wrapper
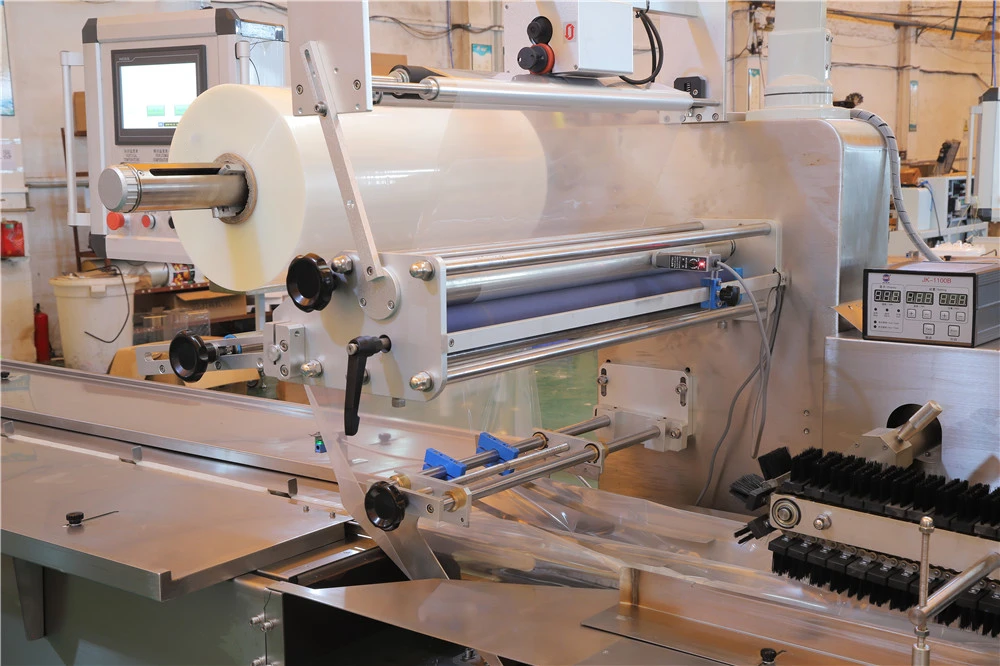
Film Roll
The roll of film is unwound from a reel and fed into the machine.
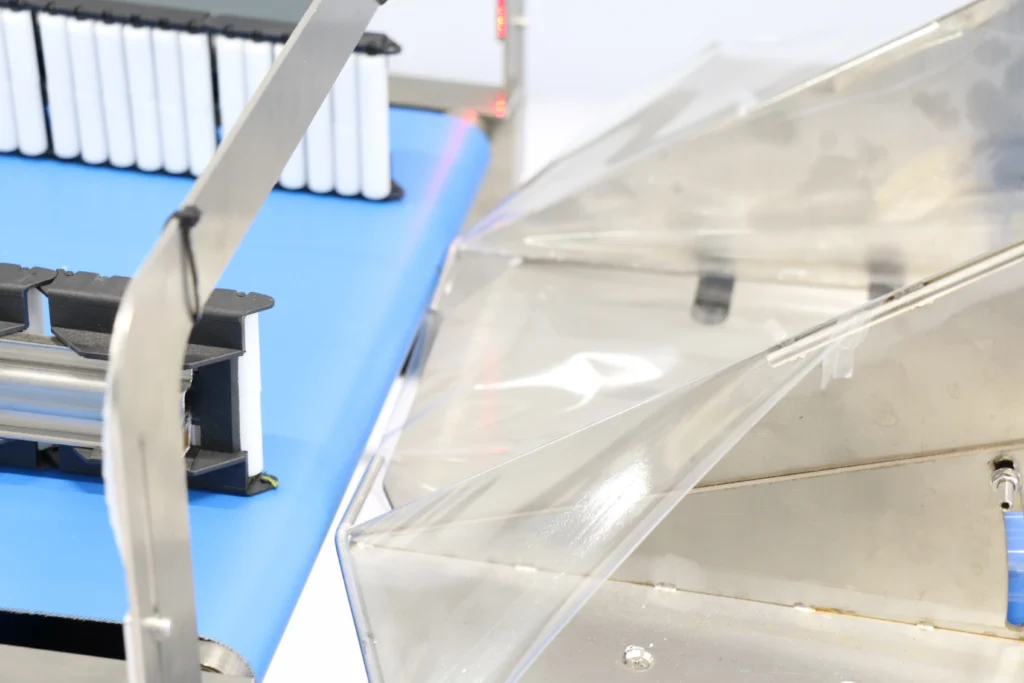
Bag Former
The film is shaped into a tube around the product using a bag former, which determines the size and shape of the package.
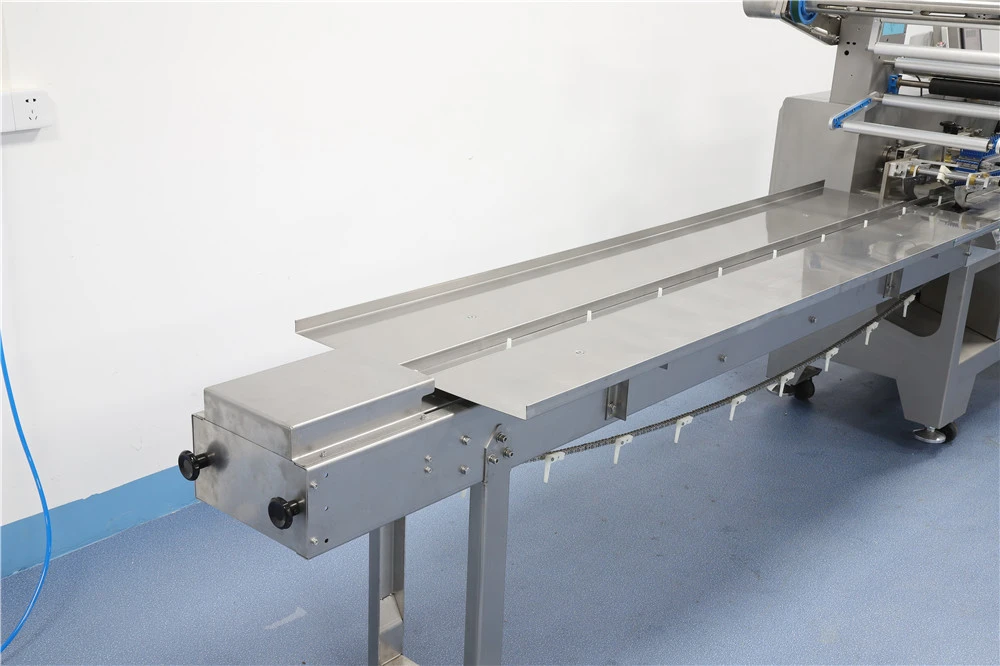
Product Infeed
The product is fed into the film tube in a continuous flow, usually by a conveyor belt.
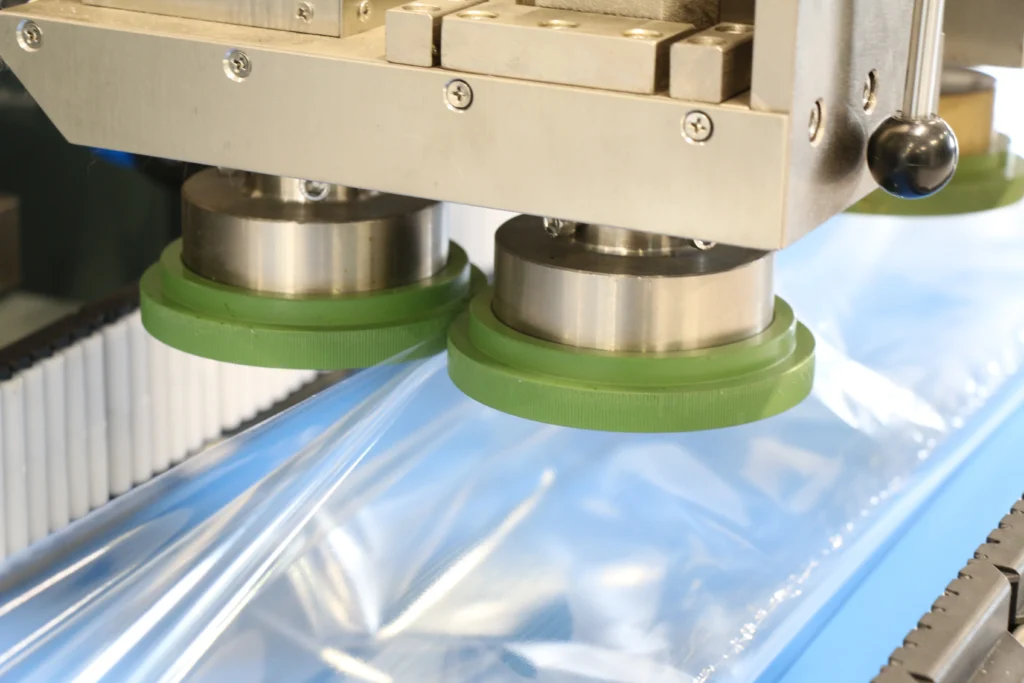
Fin wheels
The fin wheels are responsible for creating the finseal, along the sides of the package. The fin wheels grip the film, create pressure, and apply heat to seal the film together, forming a tight and secure package.
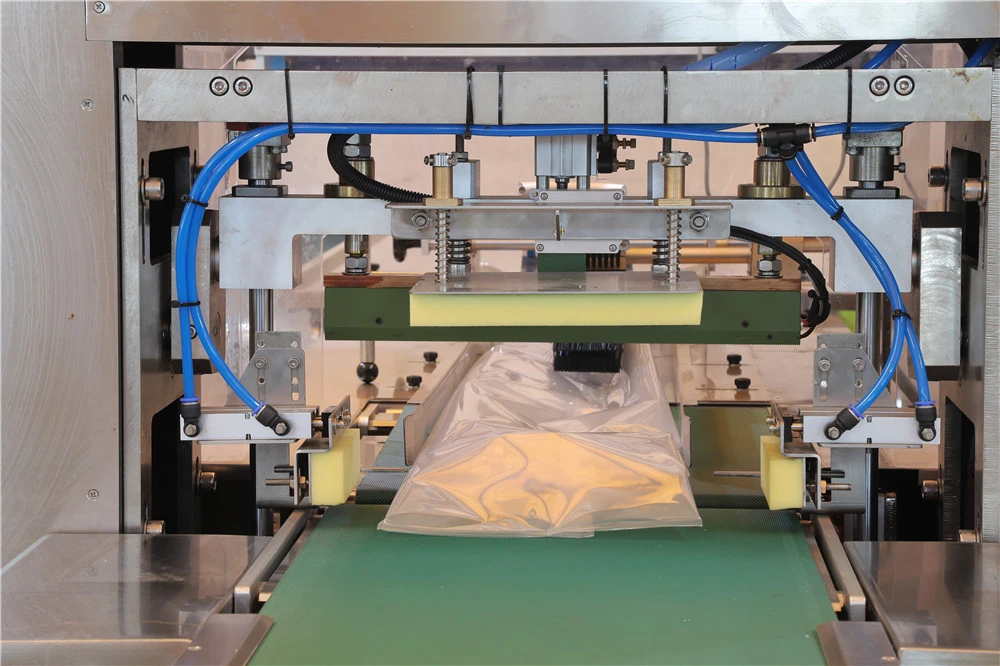
Cutting Mechanism
The cutting mechanism cuts the film between the two seals to create individual packages.
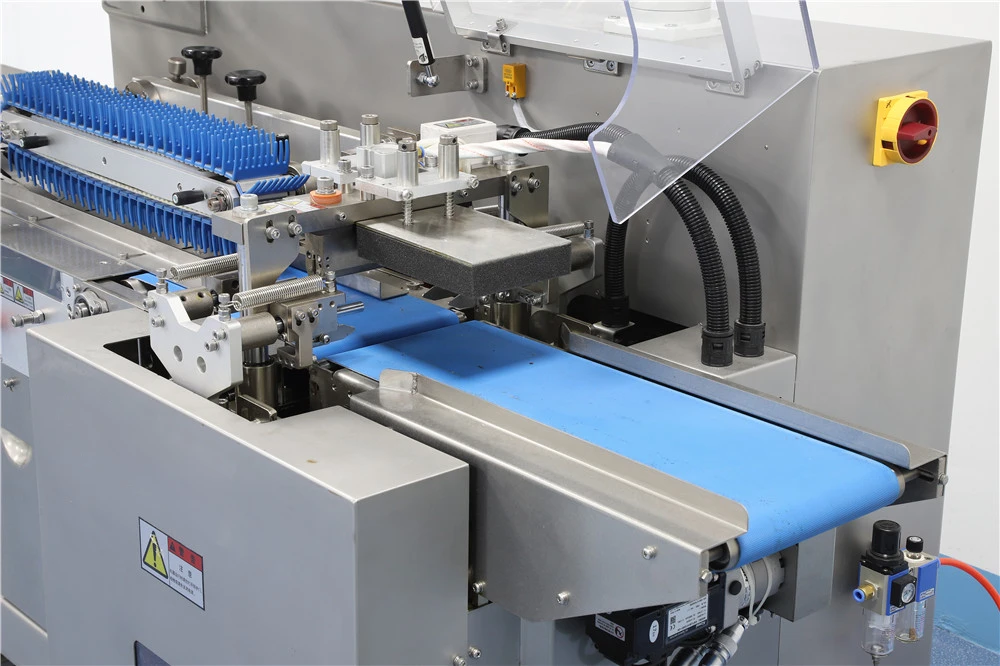
Discharge Conveyor
The finished packages are then conveyed away from the machine for further processing or packaging.
Benefits of Flow Wrapper
- Versatility
Can handle a wide range of products, accommodating various package sizes and shapes.
- High Speed
Wraps products at high speeds, designed for continuous product flow, reducing downtime and improving efficiency.
- Cost-effectiveness
Requires minimal labor and can operate for long periods with minimal maintenance, making it a cost-effective option.
- Flexibility
Highly customizable, allowing for the addition of printed labels, perforations, and easy-open features.
- Food Safety
Designed to meet strict food safety standards, washdown capability, stainless steel construction.
- Environmentally Friendly
Can use eco-friendly film materials that are biodegradable or made from recycled materials.
- Improved Product Presentation
Provides a tight, professional-looking seal that enhances the appearance of products and protects them during transport and storage.
How Does A Flow Wrapper Work
- Load the film roll into the machine and thread through the former and the product infeed.
- The product is fed into the film tube in a continuous flow, usually through a conveyor belt.
- Sealing jaws close around the film and product, creating a seal at the top and bottom of the package.
- The cutting mechanism cuts the film between the two seals to create individual packages.
- The finished packages are discharged from the machine and conveyed away for further processing or packaging.
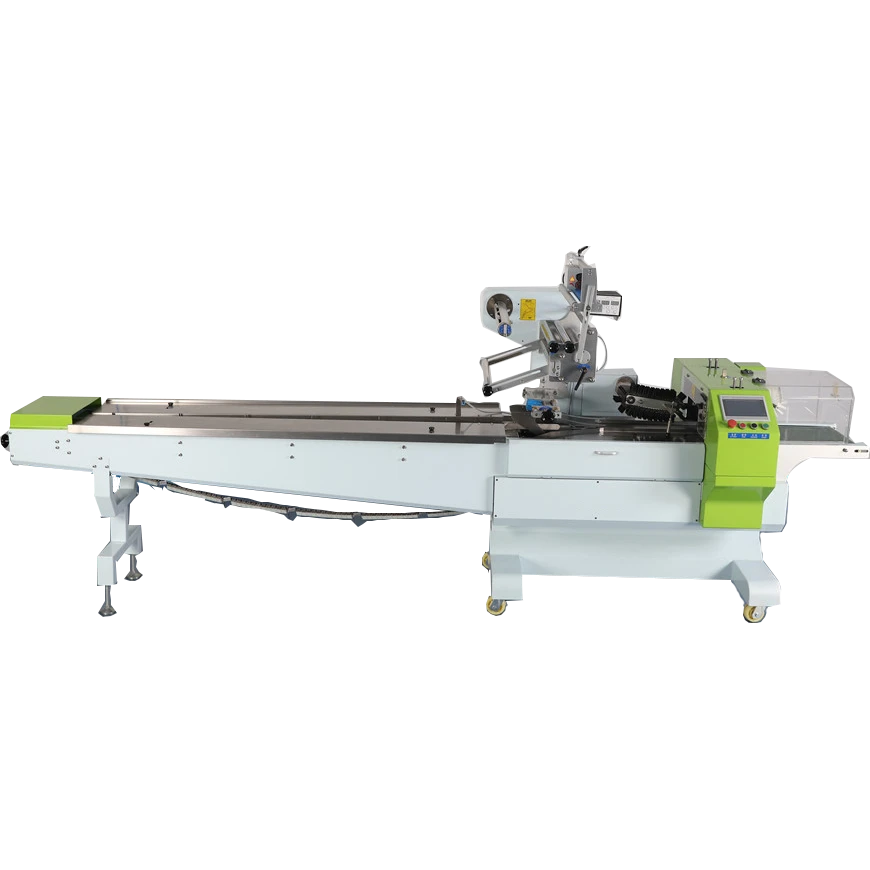
How Is Flow Wrapper Made
- 1. Design
Engineers and designers create a plan for the flow wrapper, deciding on its size, features, and how it will work.
- 2. Frame Construction
The frame is built using strong materials like stainless steel or aluminum. Pieces are cut, bent, and welded together to form a sturdy structure.
- 3. Component Assembly
Mechanical and electrical parts, like the conveyor, cutting head, and control panel, are put together and connected properly.
- 4. Control and Safety Systems
The control system, which includes a programmable logic controller (PLC) and a human-machine interface (HMI), is installed and programmed. Safety features, such as emergency buttons and sensors, are also added.
- 5. Testing and Quality Assurance
The flow wrapper is thoroughly tested to make sure it works well. Sample products are used, settings are adjusted, and performance is checked to ensure everything is up to standards.
Applications of the Flow Wrapper
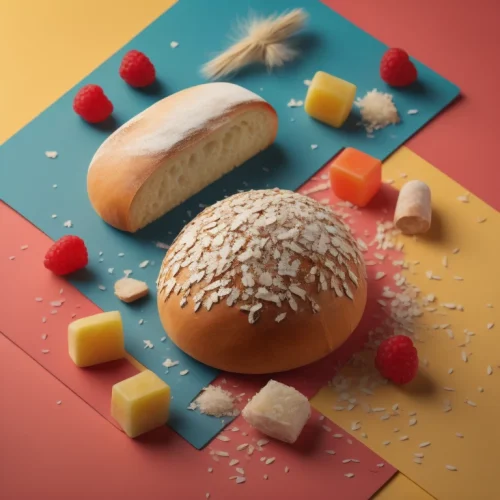
Food Packaging
Food products such as baked goods, candies, snacks, frozen foods, and fresh produce.
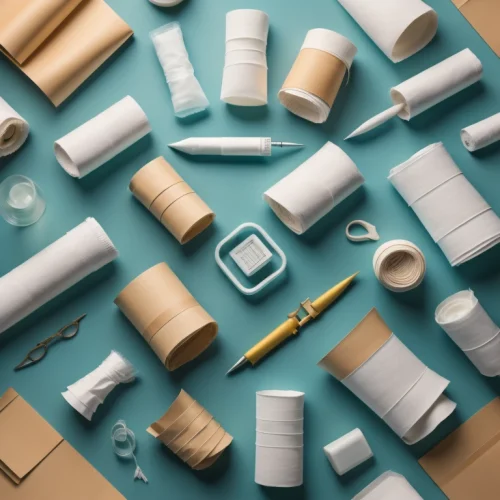
Medical and Pharmaceutical Packaging
Medical and pharmaceutical products such as bandages, gauze, syringes, and tablets.
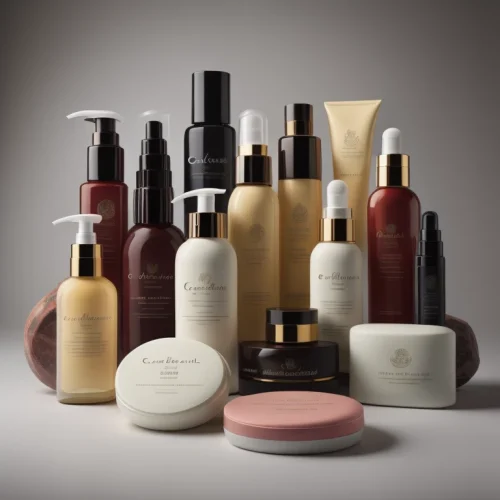
Personal Care and Beauty Packaging
Personal care and beauty products such as soaps, shampoos, and cosmetics.
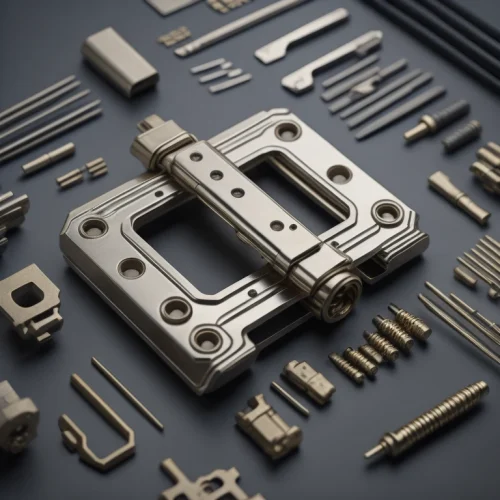
Industrial Products Packaging
Industrial products such as hardware, electronic components, and automotive parts.
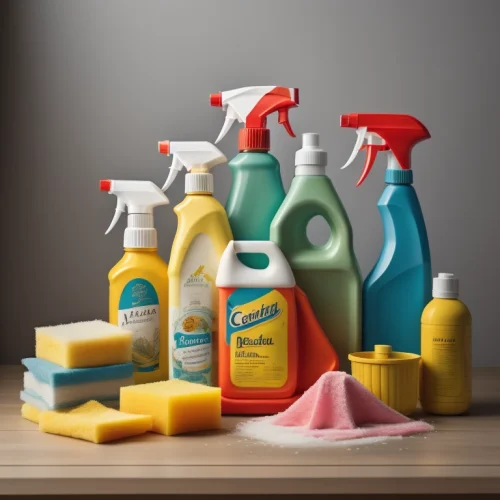
Household Products Packaging
Household products such as cleaning supplies, detergents, and pet food.
Flow Wrappers by Reel
In upper-reel flow wrappers, the film is pulled from the top of the machine and over the product before being sealed. This type of flow wrapper is typically used for packaging flat and uniform in shape products, such as candy, cookies, and other baked goods. The upper-reel design allows for a more efficient packaging process and can often wrap products at higher speeds.
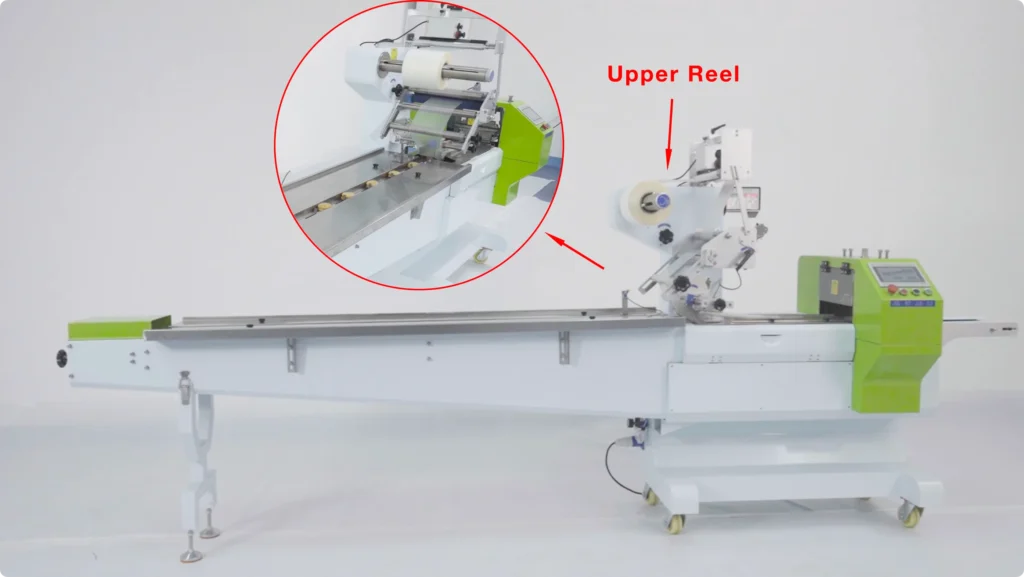
Upper Reel Flow Wrappers
In upper reel flow wrappers, the film is pulled from the top of the machine and over the product before being sealed. This type of flow wrapper is typically used for packaging flat and uniform in shape products, such as candy, cookies, and other baked goods. The upper-reel design allows for a more efficient packaging process and can often wrap products at higher speeds.
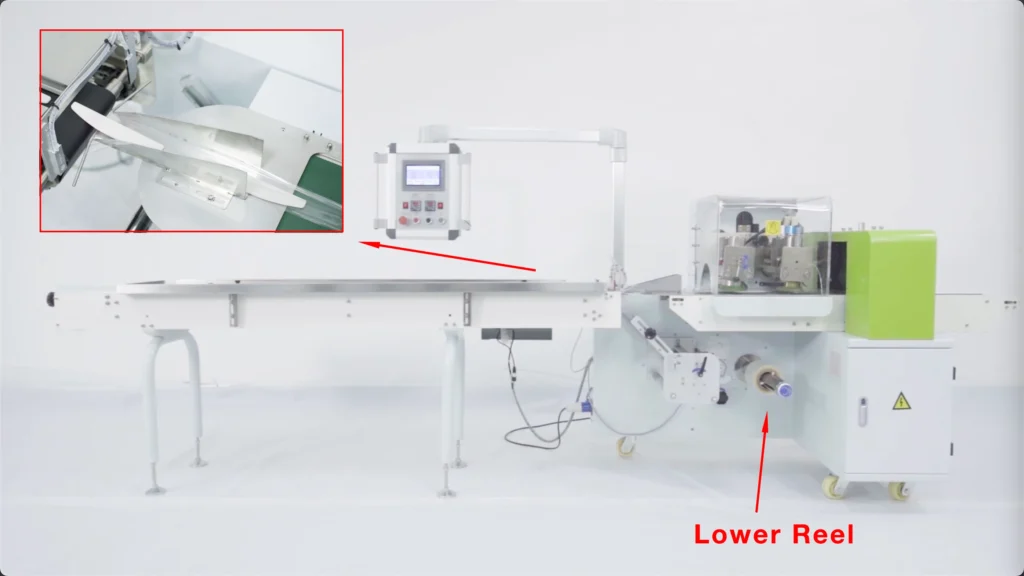
Lower Reel Flow Wrappers
In lower-reel flow wrappers, the film is pulled from the bottom of the machine and over the product before sealing. This type of flow wrapper is used to package soft, sticky, and loose products, such as meat, and cheese. The lower-reel design allows for a more stable and secure package.
Flow Wrappers by Cutting Head Configurations
Rotary Head Flow Wrappers
In rotary head flow wrappers, the cutting head rotates around the product to create the seal and cut the film. This type of flow wrapper is used for high-speed applications. It’s well-suited for wrapping smaller products like candy bars, chocolate bars, and other similar items. Rotary head flow wrappers can operate at speeds of up to 600 packages per minute. This makes them perfect for high-volume production.
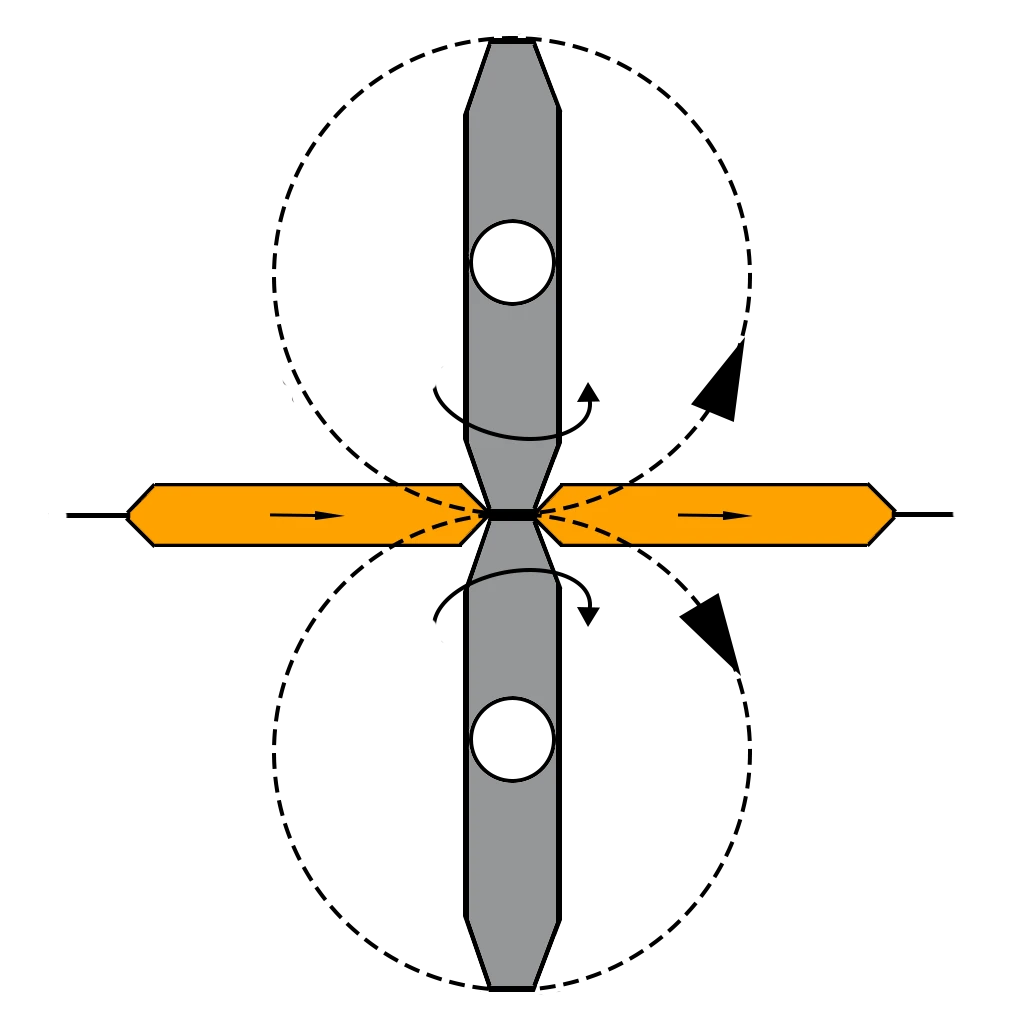
Box Motion Flow Wrappers
In box motion flow wrappers, the cutting head moves back and forth in a linear motion to create the seal and cut the film. This type of flow wrapper is used for products that require a more precise cut, such as bakery products, fresh produce, and other delicate items. Box motion flow wrappers are also well-suited for irregularly shaped products, as the linear motion allows for a more precise and accurate cut.
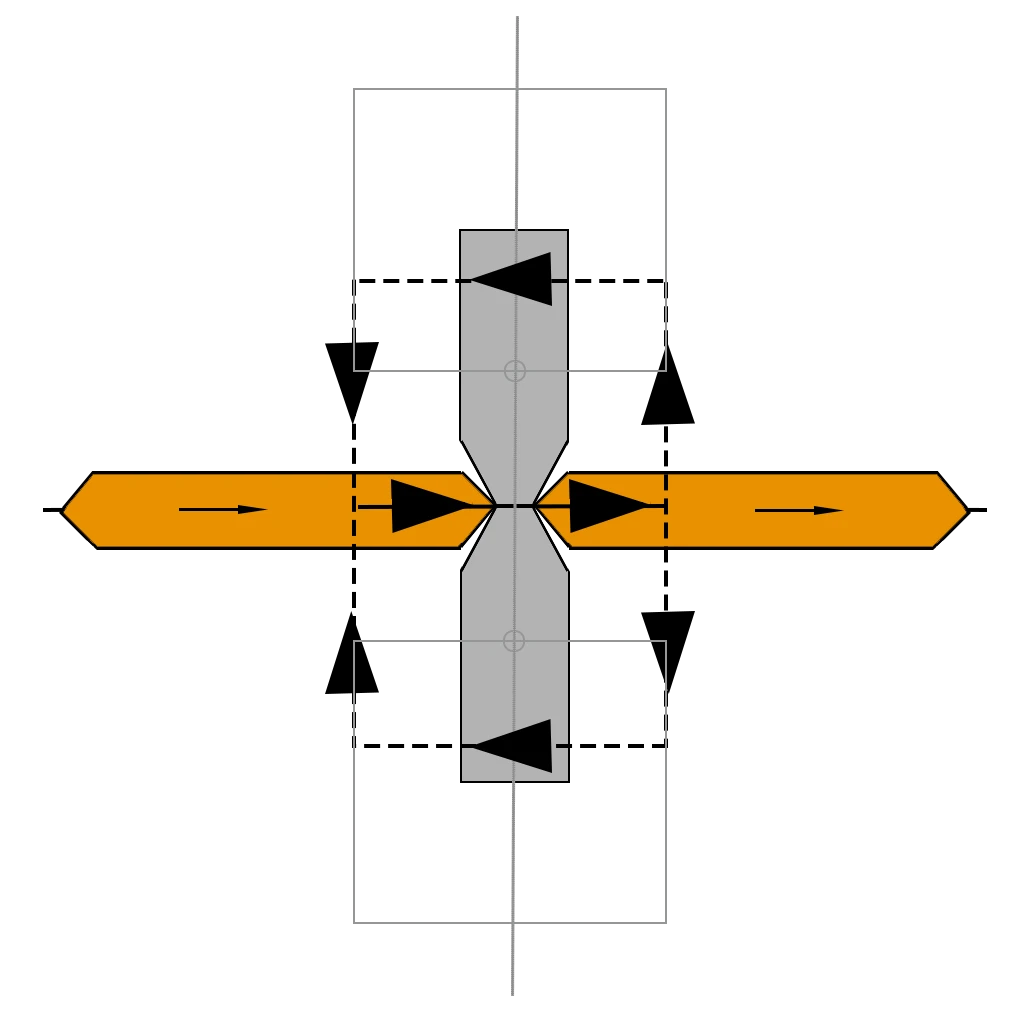
How to Choose A Flow Wrapper
- Product Characteristics
Factors such as the product size, shape, weight, and fragility will all impact the type of flow wrapper that is best suited for the job.
- Packaging Speed
Different flow wrappers have varying capabilities, so it’s important to choose one that can keep up with your production needs.
- Film Materials
Some flow wrappers can only work with specific types of film materials, so it’s essential to choose a machine that is compatible with the film you intend to use.
- Required Package Quality
Factors such as the desired seal strength, package appearance, and durability will all impact the type of machine that is best suited for the job.
- Budget
Different machines come at different price points, so it’s important to choose one that is affordable while still meeting all the necessary packaging requirements.
Troubleshooting
Problem: Products get stuck in the forming area or cutting head.
|
|
---|---|
Possible Cause
|
Solution
|
The pusher is not in step with the cutting head.
|
Adjust the package length and infeed pitch values.
|
The position of the material inside the former has changed.
|
Adjust the pressure spring or adjust the height of the support plate.
|
The cutting head is too high or too low.
|
Adjust the height of the cutting head so that the blade is positioned in the middle of the material height.
|
Problem: The film wanders and the packages wrap improperly.
|
|
---|---|
Possible Cause
|
Solution
|
The film is not centered.
|
Adjust the fine-tuning handwheel until the film is aligned on both sides.
|
The film's tension is not properly adjusted.
|
Adjust the tension of the film to make it even.
|
The bag former is too low, causing the feeding pusher to hit the film.
|
Raise the bag former until the pusher block does not touch the film.
|
Problem: The finseal isn't staying together.
|
|
---|---|
Possible Cause
|
Solution
|
The finwheel temperature is too high or too low.
|
Set the suitable finwheel temperature.
|
Poor quality of film.
|
Change a better film.
|
Dirty finwheels.
|
Clean the finwheels.
|
The gap between the finwheels is either too loose or too tight.
|
Increase or decrease the pressure between the finwheels.
|
Problem: The endseals aren't staying together.
|
|
---|---|
Possible Cause
|
Solution
|
The crimper temperature is too high or too low.
|
Set the suitable crimper temperature.
|
Poor quality of film.
|
Change a better film.
|
Dirty crimpers.
|
Clean the crimpers.
|
Crimpers mismatch.
|
Adjust the crimpers according the insruction.
|
Problem: Panel displays alarm.
|
|
---|---|
Possible Cause
|
Solution
|
Proximity switch not detected.
|
Replace the proximity switch or adjust the distance between the proximity switch and the sensing plate.
|
Color sensor not detected.
|
Replace the color mark sensor or adjust the sensitivity of the color sensor if it is not detecting the tracking point.
|
Cutter servo alarm.
|
Clear the alarm or replace the cutter servo.
|
Film feed servo alarm.
|
Clear the alarm or replace the film feed servo.
|
Feeding frequency converter or feeding servo alarm.
|
Replace the feeding frequency converter or stabilize the voltage.
|
No feeding proximity switch signal.
|
Adjust the sensitivity of the feeding photoelectric sensor, or replace the feeding photoelectric sensor.
|
No cutter proximity switch signal.
|
Adjust the position of the cutting photoelectric sensor, or replace the cutting photoelectric sensor.
|
Feeding encoder error.
|
Adjust the coupling or replace the encoder.
|
Problem: Temperature controller cannot control temperature or no display.
|
|
---|---|
Possible Cause
|
Solution
|
Heating tube or thermocouple is damaged.
|
Replace the heating tube or thermocouple.
|
Solid state relay is damaged.
|
Replace the solid state relay.
|
Temperature controller is damaged due to high or unstable voltage.
|
Replace the temperature controller.
|
Problem: Temperature display keeps jumping.
|
|
---|---|
Possible Cause
|
Solution
|
Surface of conductive copper ring is not clean.
|
Clean the conductive copper ring.
|
Poor contact between conductive copper ring and brush.
|
Adjust their positions or replace them.
|
Thermocouple short circuit.
|
Replace the thermocouple.
|
The FAQs About Flow Wrapper
How do I maintain my flow wrapper?
Regular maintenance of a flow wrapper involves cleaning and lubricating the machine, inspecting and replacing worn parts, and ensuring the machine is properly calibrated.
Can your flow wrapper be integrated into a larger packaging line?
Yes, PACKAIM’s flow wrappers can be integrated into larger packaging lines, with options for automation and synchronization with other machines.
What are some common problems that can occur with a flow wrapper?
Common problems include product jams, inconsistent product placement, film wandering, improper film feeding, and various sealing issues. You can find the solution in the manual provided by PACKAIM, or you can contact our technicians.
Can your Flow Wrapper handle different film types and thicknesses?
Yes, our Flow Wrapper can handle a variety of film types, including polypropylene, polyethylene, and laminates, as well as different thicknesses of film. Our machines are designed to accommodate a wide range of film types and thicknesses, depending on the specific requirements of the product being packaged.
Is your Flow Wrapper suitable for use in food packaging applications?
Yes, our Flow Wrapper is designed specifically for use in food packaging applications. Our machines meet or exceed all relevant food safety and hygiene regulations, and they are built with materials and components that are safe for use in food packaging.
What training and support do you offer for customers who purchase your Flow Wrapper?
We offer comprehensive training and support to all of our customers who purchase our Flow Wrapper. This includes initial operator training, as well as ongoing technical support and troubleshooting assistance.
Ready to Elevate Your Packaging Efficiency
Leave a Message Now and Discover How Our State-of-the-Art Flow Wrappers Can Transform Your Business!