Boosting Productivity with Automated Carton Packing Machines
Table of Contents
Introduction
Hey friends! As a sales on cartoning machines, I get a lot of questions about how companies can improve efficiency in their packaging lines. I’m here to share my insider knowledge on how automated carton packing machines can seriously boost output and lower costs.
In this post, I’ll give a crash course on different types of carton packing machines, key features to consider, and real-world examples of companies that benefited from automation. My goal is to explain the benefits in a simple, conversational way – no fancy jargon!
Whether you’re looking to reduce labor, increase speed, or gain flexibility, automated case packing is the way to go. Read on to learn how these smart machines can transform your packaging operation!
Types of Carton Packing Machines
There are two main types: horizontal and vertical carton packing machines. Let me break down how each one works:
Horizontal Carton Packing Machines
Horizontal carton packing machines use a straight-through design to load products into boxes. Cartons are put together, sealed with hot melt glue, and moved through the machine. Products are grouped and inserted horizontally as boxes pass by.
These flexible machines can handle different counts of products per carton. Horizontal cartoners need a good amount of floor space but make changeovers a breeze. They’re great for medium-sized products.
Vertical Carton Packing Machines
Vertical cartoners operate top-down for super high speeds. Erected boxes stay locked in position while products drop down from above. Servo motors precisely meter products into cartons in vertical stacks.
Vertical carton packing machines have a small footprint and excel at max throughput. They need minimal changeover time between box formats. If you’ve got high volumes of uniform products, vertical cartoners are ideal.
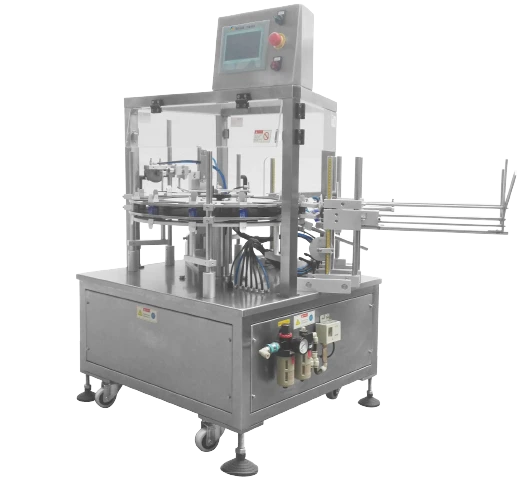
Choosing between horizontal and vertical depends on your products, speeds, box sizes, line layout, and more. I suggest talking to experts to pick the right system.
Key Features of Carton Packing Equipment
Let’s look at some of the most important capabilities that make modern case packers so efficient:
Speed and Throughput
Blazing speed is a must for high-volume packaging. Today’s cartoning machines use advanced components like servo drives, robotic pick-and-place, and slick product feeds to hit crazy fast rates – we’re talking 60 to 100+ cartons per minute!
High-performance motors and motion control blast through packaging cycles with barely any downtime. Some systems can even sync with other equipment for seamless automation. For maximum efficiency now and in the future, get a case packer sized above your current needs.
Flexibility and Adjustability
To keep up with changing products and packages, your cartoner needs built-in flexibility. Key adjustments include:
- Box size changeovers – Tool-free parts swaps adapt the machine for different carton sizes fast.
- Product loading – Adjustable feeds group and load products smoothly.
- Packing patterns – Programmable for different product arrangements.
- Modular components – Easily integrate scales, sealers, conveyors, and more.
I look for quick-change guides, user-friendly controls, and recipe presets that make changeovers a cinch. The more range in the machine, the more packaging options down the road!
Benefits of Automated Carton Packing
Switching from manual case packing to automation has big advantages:
Increased Output and Efficiency
Unlike humans, automated cartoners pack cartons nonstop at full speed for entire shifts. Intelligent features like servo drives and auto-glue minimize downtime too. I’ve seen companies increase output by 20-40% easily after installing case packers! The machines also improve overall efficiency with more products packed per person per hour. It’s a night and day difference vs hand packing.
Reduced Labor Costs
Automating case packing means you’ll need way fewer workers on the line. One case packing machine can replace up to 4-8 manual packers. Huge labor cost savings! Automation also improves safety by removing repetitive motion tasks that can cause injuries over time. The latest robotic case packers even automate the loading and unloading. With a good cartoner, you can get by with just 1-2 operators instead of a huge crew.
Integrating Carton Packing Machines into Workflows
To get those sweet efficiency gains, you’ve got to properly integrate your shiny new carton packing machine with the rest of the line:
Conveyor and Line Integration
Well-designed conveyors are key for smooth product transfers and sequencing into the cartoner.
Clever layouts accurately group and pace items into the machine. Smart controls perfectly match the conveyor and cartoning machine speeds for seamless hand-offs. Top systems can automatically adjust feed rates if the cartoner slows to prevent jams. Outbound conveyors need to connect properly to case erector, case packer, case sealer, palletizers, and more downstream.
Work with integration experts for optimal cartoner transitions.
Sensors and Scanning
Sensors make automation possible by acting as the eyes and ears of the machine. Photosensor verifies that products are sequenced and grouped properly. Vision systems confirm product counts entering cartons.
Barcode scanners enable quick recipe and size changeovers. Sensors also track box inventory, flag low glue, monitor operation, and more. The more sensors, the more responsive the system.
Look for cartoners with built-in sensor ports and capabilities. It’s smart to install extras upfront as your needs grow.
Purchasing Considerations for Carton Packers
Some key factors in choosing an automated case packer:
Required Output and Speed
Think about current and future production volumes needed in cartons per minute.
Oversizing capacity adds unnecessary costs. Undersizing risks bottlenecks as you grow. Look for output 25-50% above your present needs – this allows room to expand without paying for unused speed.
I suggest planning space for multiple machines if your volumes eventually require it. Discuss staging and expansion with suppliers.
Box Sizes and Adjustability
Know the range of carton sizes and dimensions you need to run now and in the coming years. Wider adjustment ranges equal more packaging flexibility.
Compare changeover times and mechanical effort between brands. Toolless or quick lock changeovers are ideal for maximizing uptime.
Systems needing extensive retooling or changing parts cost more production time. Quick release guides, power adjustments, and recipe presets make size changes fast and simple.
Consider extended side guides for undersized cartons. Talk through any unique box sizes needed.
Real-World Examples and Success Stories
Here are a couple of real-world case studies of companies that boosted efficiency with automated carton packing machines:
Case Study 1
A big candy company was manually packing gift boxes and assortments at 30-40 cartons per minute. They installed a top load cartoner with automated infeeds, hot melt sealing, and outfeed conveyors. The flexible machine handles a wide range of candy box sizes with quick changeovers.
Output increased by over 50% to 60 cartons per minute with the new carton packing machine. Even better, they cut labor by 70% since the whole process is automated end-to-end. The adjustable cartoner easily switches from everyday packs to seasonal assortments with no downtime.
Case Study 2
A pet food manufacturer was hand packing kibble bags and canned foods at high labor costs. They brought in a horizontal cartoner capable of packing products in various configurations from 1×4 to 4×4. High speed servo drives and smooth product handling allowed continuous rates up to 35 cartons per minute.
The new machine chopped their carton packing labor needs by 5 workers, a 40%+ cost reduction! The flexible cartoner adjusts across box and bag sizes with simple change parts, no tools are required. Reliable operation increased overall output by 30% without adding any staff. The versatile pack patterns also created opportunities for new multipack offerings.
Conclusion
There you have it friends – the inside scoop on transforming your packaging with automated carton packers!
Whether horizontal or vertical, integrated smart carton packing machines with quick changeovers can massively increase output, lower labor, and improve flexibility.
Companies regularly see 20-40% productivity gains and major cost savings after switching from manual to automated packing. The machines pay for themselves quickly with all the efficiency benefits.
Hopefully, this gives you a helpful overview of the possibilities for your production line. Let me know if you have any other questions!
Jason
I’m the author of this post, with over 10 years of expertise in the field. Should you seek insights or information about automatic cartoning machines, I’m here to assist. Let’s connect and explore the world of packaging together.