The Complete Guide to VFFS Machines
Vertical form fill seal (VFFS) machines revolutionized the packaging industry by offering an efficient, automated way to create customized bags and pouches.
With speed, flexibility, and reliability, it’s no wonder VFFS systems are ubiquitous across food, pharmaceutical, and consumer goods manufacturing.
In this comprehensive guide, we’ll unpack everything you need to know about VFFS packaging equipment, including how these versatile machines work, their key components, available configurations, and ideal applications. Let’s get started!
What Are VFFS Machines and How Do They Work?
- Forming the film into a vertical tube around a product chute
- Sealing the bottom edge to close the bag bottom
- Filling the bag with product through the chute
- Sealing the top and cutting off the finished bag
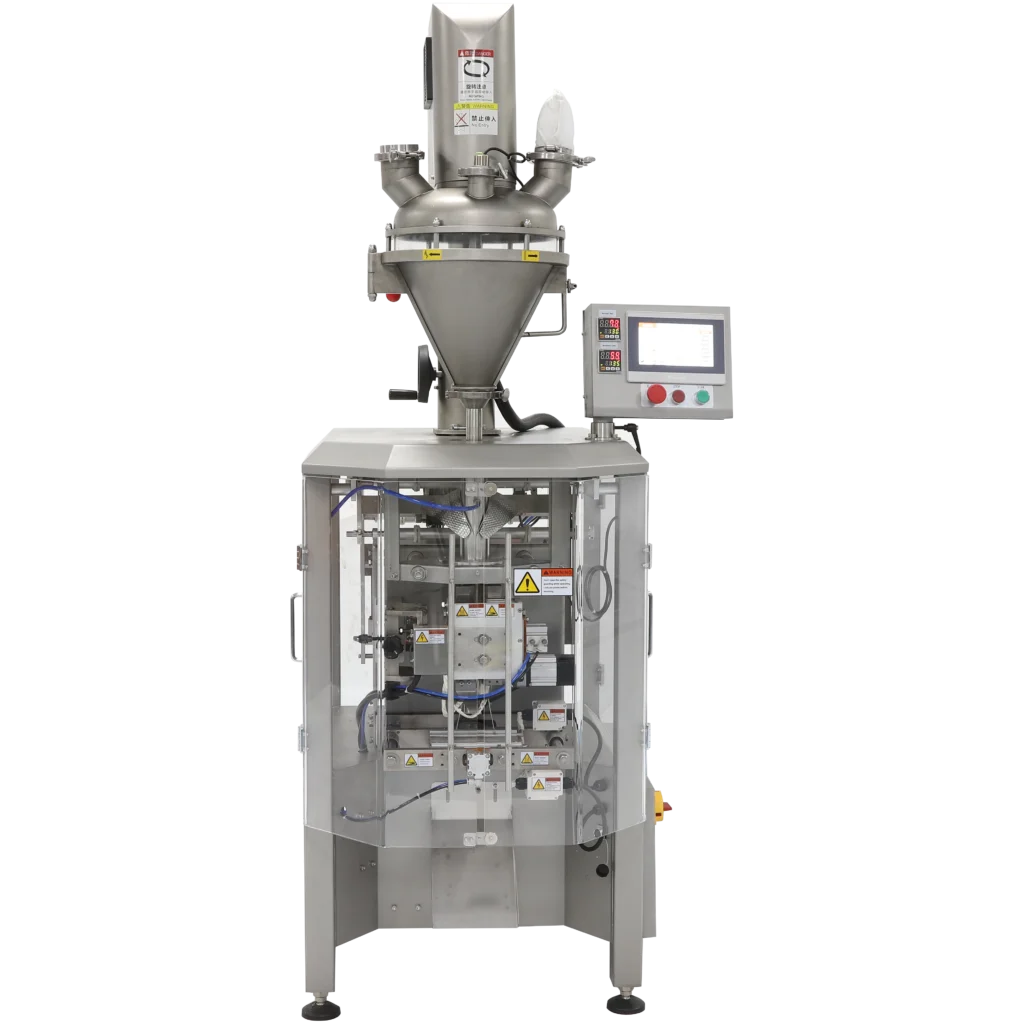
This automated process allows the rapid production of customized bag shapes, styles, and sizes based on the product needs.
Here is a step-by-step overview of the VFFS packaging process:
- Packaging film is unwound from a roll and guided around a forming shoulder into a vertical tube shape.
- The vertical tube is heat sealed along the bottom edge to form the bag bottom. Often two parallel seals are created with a perforation in between, allowing for easy separation later.
- Product is dispensed from a hopper through the product chute and fills the bag to the desired amount. Volumetric augers, vibratory feeders, or pumps can meter powders, liquids, and granular products.
- Sealing jaws close on the tube to create a top seal and bottom seal for the filled bag. The top seal also separates the finished bag from the film tube.
- A cutting mechanism trims any excess film above the top seal. Conveying systems then transport the finished bag away.
- The film tube instantly re-forms around the product chute and the cycle repeats continuously at rapid speeds to create hundreds of filled bags per minute.
This fully automated process minimizes human involvement for fast, efficient packaging. Now let’s look at the key components that make up VFFS systems.
Critical Components of VFFS Machines
Though designs vary, most VFFS packaging equipment contains the following components:
- Film Roll – Holds a continuous roll of packaging film. Common materials include polyethylene, polypropylene, and laminated films. An automated splicer can splice new film rolls for continuous operation.
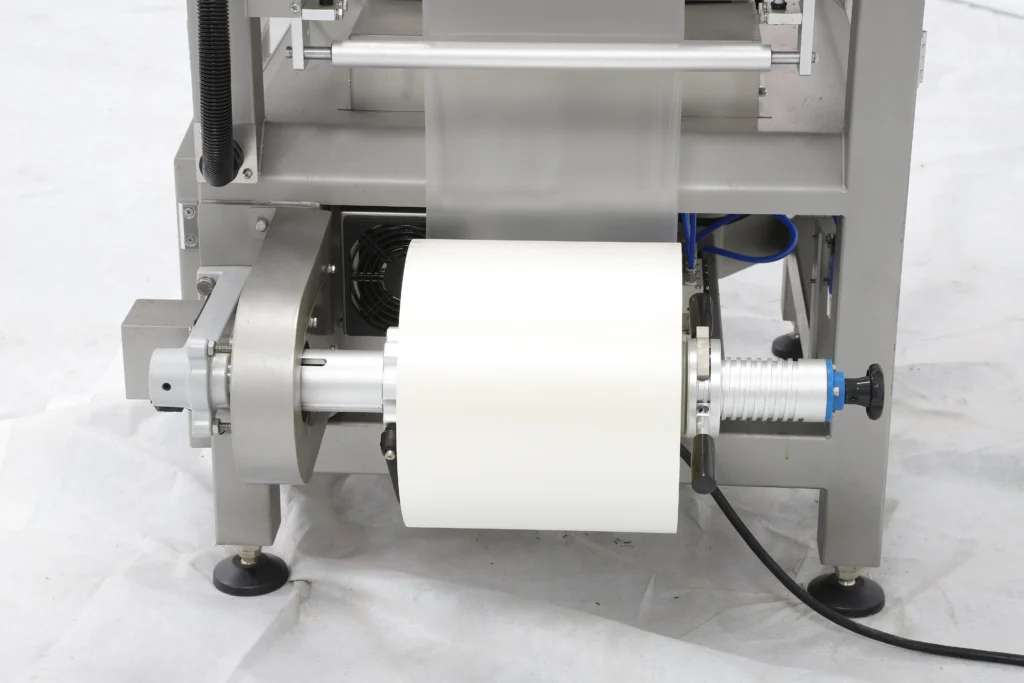
- Film Drive – Feeds the packaging film into the machine. Typically incorporates servo motors for precise speed control.
- Forming Shoulders – Guide the flat film into a vertical tube around the product chute.
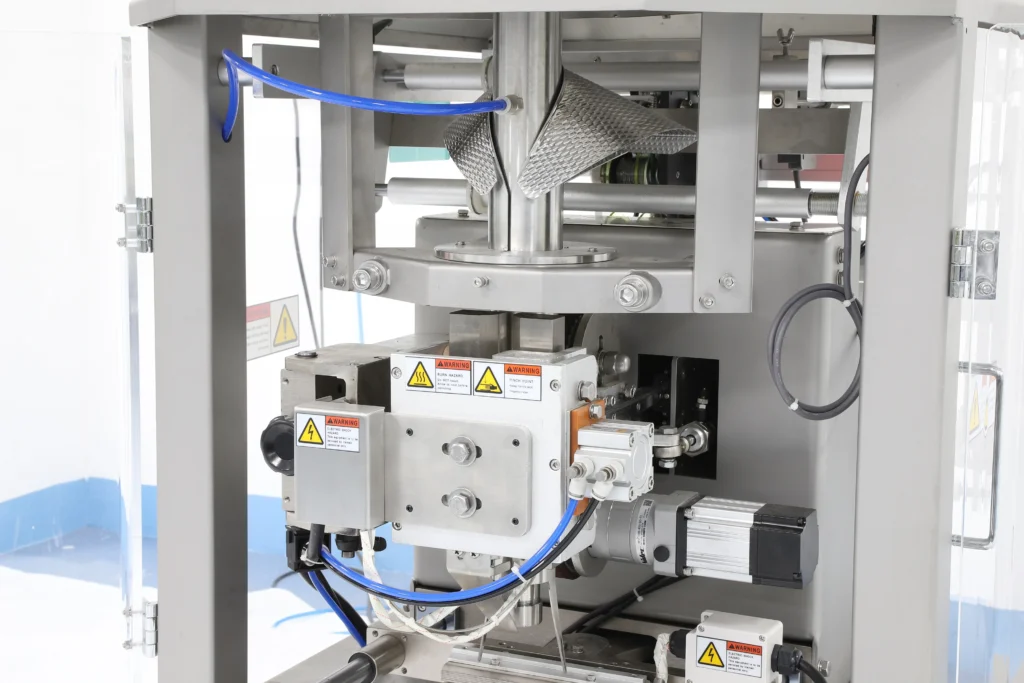
- Longitudinal Sealer – Seals the overlapping edges of the packaging film to form a tube. Often a heat seal bar.
- End Sealing Jaws – Seal across the tube to create bottom and top seals for each bag. Often heated jaws or bands.
- Cutting Mechanism – Trims the film between finished bags. Can be heat seal, mechanical knife, or other method.
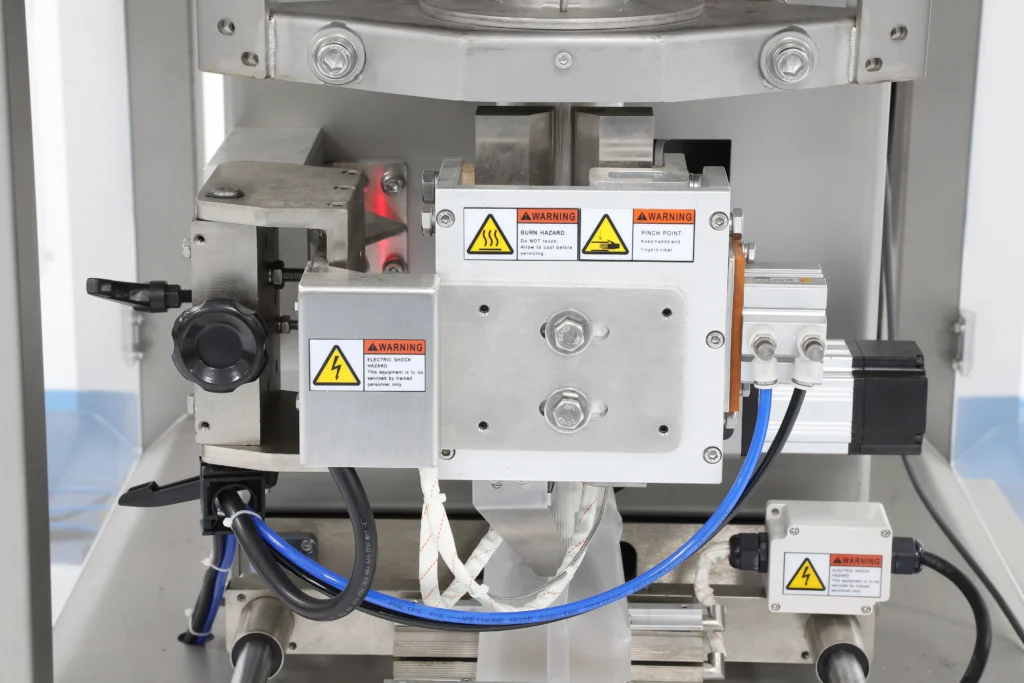
- Product Chute/Funnel – Vertical tube where product is dispensed into bags.
- Product Dosing – Volumetric augers, vibratory feeders, pumps, or scales to meter product into each bag.
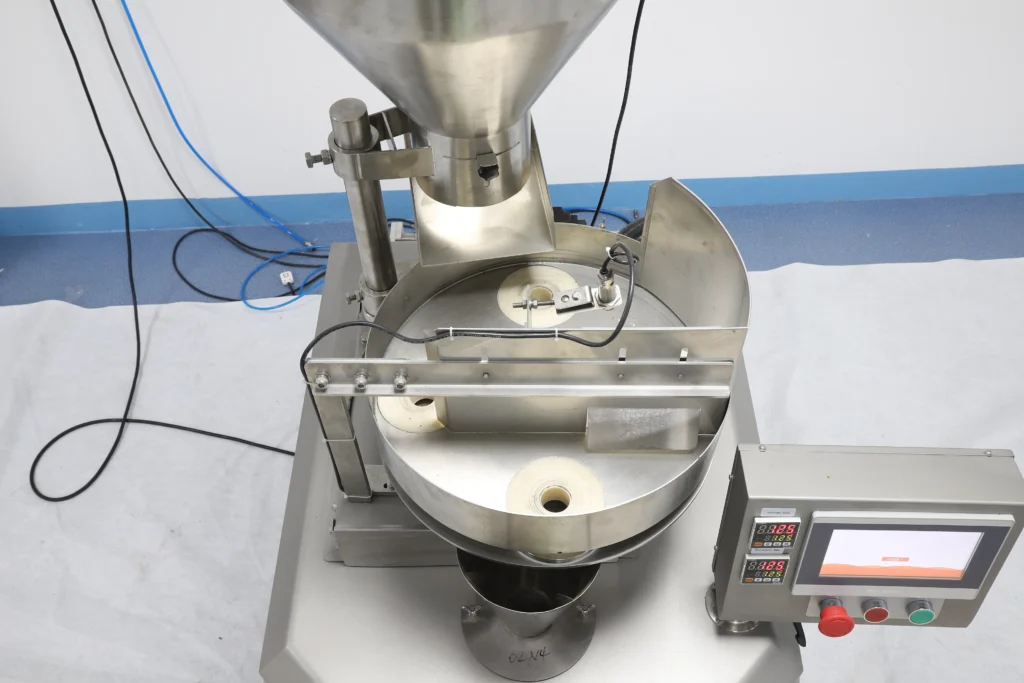
- Discharge Conveyor – Transports finished bags out of the machine.
- PLC Controls – Programmable logic controllers sequence machine operation and allow integrate with other equipment.
- HMI – Human-machine interface with touchscreen for controlling the VFFS system.
These components work in orchestration to form, fill, seal, and cut individual bags at high speeds. Next we’ll look at the benefits VFFS machines offer.
Key Benefits of VFFS Packaging Systems
There are many good reasons VFFS packaging equipment has become ubiquitous for flexible packaging across industries. The main benefits include:
High Speed and Efficiency
VFFS machines produce filled and sealed bags at rates from 10 to 100+ per minute, vastly outpacing manual packaging. The automation streamlines the packaging process for improved labor efficiency.
Flexibility and Versatility
With quick changeover VFFS baggers can handle a wide range of bag sizes, shapes, features, and materials. This flexibility suits the needs of diverse and frequently changing products.
Cost Savings
By automating the packaging process, VFFS bagging machines reduce labor costs. Less film waste compared to pre-formed bags also helps minimize material costs.
Improved Product Quality and Shelf Life
The consistent fill control and sealed packaging of VFFS systems maintains product quality and extends shelf life. Rejects and waste are minimized.
Compact Footprint
All-in-one VFFS packaging equipment condenses the entire packaging process into a compact footprint. This saves valuable factory floor space.
Sanitary Design
Stainless steel components and washdown construction allows VFFS machines to meet strict hygiene requirements for food, pharmaceuticals, and medical devices.
With those benefits covered, let’s move on to the available configurations of VFFS systems.
Types of VFFS Machines Configurations
While VFFS machines share the same core functions, there are some key variations in machine design:
Flat Film vs. Tube Film
- Flat film VFFS starts with packaging film in flat roll form. The film is formed around a tube on the machine itself.
- Tube film VFFS utilizes preformed film tubes and only has to seal the ends. Simpler design but less flexible.
Machine Orientation
- Horizontal VFFS systems have film fed in perpendicular to the product chute. Takes up more floorspace but allows larger bags.
- Vertical VFFS machines feed film down in line with the product chute for reduced footprint. Smaller maximum bag size.
Bag Styles
- Pillow bags are simple rectangular bags, ideal for loose powders and products.
- Gusseted bags have folded side regions that expand when filled. Allow for higher volume capacity.
- Shaped bags can have contours and fit specific product shapes.
- Four side seal bags are sealed on all four sides, avoiding open edges. Good for aseptic packaging.
Bag Features
- Zippers, spouts, handles, and other features can be integrated using specialty films and machine tooling.
Machine Size
- Compact tabletop systems for R&D and small production runs.
- Large industrial VFFS for high volume packaging lines.
- Customized layouts to suit product and space needs.
This range of configuration options makes VFFS equipment ideal for diverse packaging requirements across all types of industries.
Applications and Industries Using VFFS Machines
Given their versatility, it’s no surprise VFFS packaging systems are extensively used across many industries:
Food and Beverage
For packaging dry goods, powders, snacks, produce, frozen foods, baked goods, and more. Sanitary designs meet food safety regulations.
Pet Food
For kibble, treats, and wet pet foods. Durable bags with handles and spouts.
Pharmaceuticals
Sterile designs for pills, medical powders and liquids. Validation compliant.
Industrial and Hardware
VFFS bags ideal for nuts, bolts, hobby supplies, crafts, and more.
Personal Care and Cosmetics
Powders, creams, soaps, and beauty products nicely packaged in pillow, gusseted, and shaped bags.
Essentially any loose solid products that need light-weight, shelf-stable containment are perfect candidates for VFFS packaging. Even liquid products can be packaged using specialized spouted bags and dosing systems.
For high speed, automated packaging of diverse products, it’s hard to beat the flexibility and efficiency of vertical form fill seal machines!
Choosing the Right VFFS Machine
When selecting VFFS packaging equipment, consider factors like:
- Desired bag styles, sizes, features, and film material.
- Product characteristics like shape, weight, density, and flowability.
- Required output rates and changeover times.
- Available floor space and production environment.
- Integration with upstream and downstream equipment.
- Options like bag printing, hole punching, nitting, etc.
- Budget constraints and total cost of ownership.
Leading VFFS manufacturers offer custom-configured machines tailored your unique specifications and production needs. Collaborating closely with the packaging equipment supplier is key to getting the best solution.
Conclusion
With benefits like high speed, flexibility, and reliability, it’s easy to see why VFFS is the go-to packaging method across so many industries. These automated all-in-one machines streamline the packaging process to maximize efficiency.
I hope this guide provided you with a comprehensive overview of VFFS packaging systems.
Please reach out with any other questions! I’m always happy to chat more about vertical form fill seal technology and finding the ideal VFFS machine for your production needs.
Jason
I’m the author of this post, with over 10 years of expertise in the field. Should you seek insights or information about VFFS machines, I’m here to assist. Let’s connect and explore the world of packaging together.